FAQs
Ensuring data security is TDK SensEI’s top priority. edgeRX implements System and Organizational Control 2 (SOC 2) whose key components are:
- Security: Protecting system resources from unauthorized access
- Availability: Ensuring system uptime and operational continuity
- Processing Integrity: Maintaining data accuracy and completeness throughout processing
- Confidentiality: Protecting sensitive customer data from unauthorized disclosure
- Privacy: Managing personally identifiable information (PII) according to privacy regulations
In addition to SOC 2 compliance, TDK SensEI employs additional security measures:
- Data from manufacturing environments are encrypted in transit and at rest
- Sensors are white-listed so that a non-provisioned device will not connect to the Gateway
- No PII (Personally Identifiable Information) collected or stored
- Key data is tokenized
- Customer data is segmented and logically isolated (support for multi-tenancy) in cloud
edgeRX is an advanced machine health monitoring solution designed to enhance industrial equipment monitoring and maintenance. It leverages cutting-edge AI to provide predictive maintenance capabilities, ensuring optimal performance and reducing downtime.
To learn more, please visit our edgeRX overview blog.
The edgeRX Sensor is a cutting-edge wireless device designed to revolutionize machine health monitoring. With its impressive three-year battery life, this sensor eliminates the need for frequent maintenance, making it a cost-effective and reliable solution for long-term deployment. It collects and analyzes critical data such as vibration, temperature, and other performance meterics, enabling real-time insights into machine health. By leveraging advanced computing capabilities, the edgeRX sensor processes data locally, reducing latency and ensuring rapid detection of anomalies or potential failures. Its compact and durable design allows it to be seamlessly integrated into various industrial environments, providing organizations with a scalable and efficient tool to optimize equipment performance and minimize downtime.
It is FCC, CE, SRRC, and TELEC compliant.
It is equipped with:
MCU: Nordic nRF5340
Accelerometer: IIM42652
Temperature Sensor: SHTC3
Communication: BLE 5.0 supported
Flash: 64Mbit QSPI flash for local data storage
Battery: 1000mAh Li battery (replaceable)
IP Rating: IP67
ODR: Up to 8K (BLE only)

The edgeRX Gateway is an advanced connectivity hub designed to seamlessly integrate with the edgeRX Sensor for comprehensive industrial machine health monitoring. Equipped with 4G LTE, WiFi, and BLE 5.0 communication technologies, the gateway ensures reliable and flexible data transmission, whether operating in remote locations or within complex industrial environments. It serves as the central bridge, aggregating data from multiple edgeRX Sensors and securely transmitting insights to cloud platforms or on-premises systems for further analysis and storage. The gateway's robust design enables real-time monitoring and decision-making, while its compatibility with various communication protocols makes it highly adaptable to diverse industrial setups.
It has a 120M BLE range and is FCC/UL, CE, SRRC, and TELEC certified.
It is equipped with:
CPU: MCIMX6Y2DVM05AA, ARM Cortex-A7,528MHz
Memory: 512 MB DDR3 RAM, 4GB eMMC ROM
Ethernet: 10/100M Ethernet
Wireless Communication: 4G-LTE (Configurable), WiFi (Configurable), BLE 5.0
RS485: Modbus (optional)
LED: 5 * Green LED (System, BLE, RS485, Ethernet, 4G and WiFi)
Button: Factory reset (long press > 5sec), BLE Pairing (short press)
USB: 1 * USB 2.0 (optional)
Power Supply: Typical 12V DC input, range from 9V~36V, Support PoE (IEEE 802.3af, 13W maximum) Configurable
IP Rating: IP67
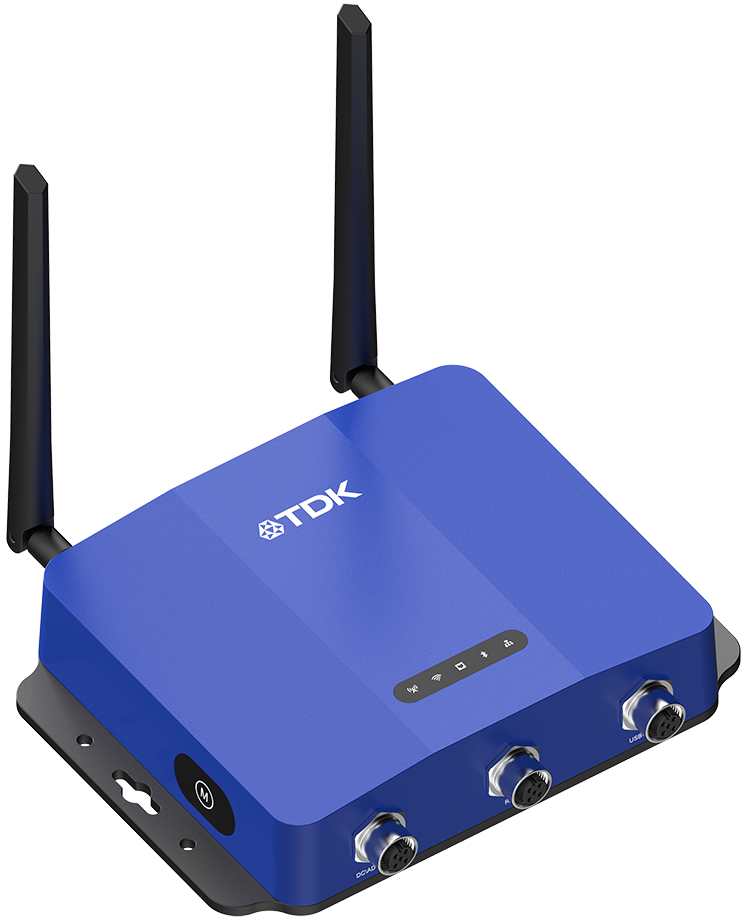
No, edgeRX only collects data from sensors and does not collect private data about users or their company. Data is also encrypted while in transit and at rest.
edgeRX AI is trained on sensor collected data that is analyzed in the cloud. Firmware and AI model updates are passed through the gateway which then transmits the data to the sensors. AI on these devices will continuously infer upon machine health live at the source. Depending on the needs of the user, AI models can be quickly passed to devices to calibrate sensitivity.
Condition-Based Monitoring (CbM) is a maintenance strategy that involves analyzing data from machines and inferring degradation or failure. It aims to identify where machines break down and reduce unplanned downtime and repair costs.
Key Aspects of Condition-Based Maintenance:
- Real-Time Monitoring
- Artificial Intelligence Training
- Classification of Anomalies
Benefits of CbM:
- Reduced Downtime
- Reduced Costs
- Improved machine lifespan and efficiency
To learn more about our CbM solution, edgeRX, check out our blog.
edgeRX predicts machine health states by analyzing trends over time. Users can monitor defined machine states and their degradation. As edgeRX AI collects data over extended periods, it assesses its own reliability and effectiveness, making adjustments for future analyses.
edgeRX’s edge AI can identify additional fault states outside of conventional ISO frameworks, providing users with deeper insights into the condition of their machines.
This advanced capability allows for comprehensive monitoring and proactive maintenance, ensuring optimal machine performance.
TDK factories around the world are already reducing substantial maintenance costs using edgeRX as their maintenance strategy.
To see one such example please see our case study.
edgeRX sensors can detect vibration and temperature even in environments with extraneous noise. This includes equipment such as motors, pumps, and reciprocal machines. The AI inference of these can be indicative of certain faults such as imbalance, looseness, lubrication, and cavitation.
Yes, once a healthy baseline operational dataset is established, fault-states can help train the AI on what anomalies look like. edgeRX is capable of detecting multi-class anomalies in its environment and is able to distinguish between operational, idle, and faulty machine states.
Edge AI is a type of artificial intelligence that operates at the source of data collection (the edge), i.e., machines. This removes the need for a continuous internet connection, reducing bandwidth and power consumption needs. The AI within the sensor can alert the manufacturing system when asset failure occurs.
For users who operate with older equipment, edgeRX can easily be deployed to manage, maintain, and extend machine lifespans. edgeRX can also be used to enhance existing AI maintenance systems that may not have adequate coverage or capabilities.
No, edgeRX is designed to custom train AI for each machine in an industrial ecosystem. While similar machine datasets can be shared to enhance training, each deployed AI on a sensor will be intelligently monitoring their assigned machines. This allows edgeRX the flexibility to scale with any environment.
The edgeRX dashboard is low touch and allows users to configure operation label detection, anomaly detection frequency alerts, and parameter sensitivity. With its user-friendly interface, users can create ready-to-use models in minutes, all without needing any coding knowledge. Users from anywhere can also access the cloud-based dashboard or use one of TDK SensEI’s open APIs to integrate with existing infrastructure.
Analyzing time-series data, edgeRX AI can either use existing customer collected data or start collecting new data to build AI models. Data collection/analysis may take up to two weeks before a model is ready to deploy.
Users will see available AI models for deployment in 1-2 weeks after sensor installation. The edgeRX dashboard can configure anomaly detection frequency and can display equipment health in real time.